碳化硅單晶具有極高的硬度和脆性,傳統(tǒng)加工方式已經(jīng)不能有效地獲得具有超高光滑表面的碳化硅晶片。針對碳化硅單晶襯底加工技術(shù),本文綜述了碳化硅單晶切片、薄化與拋光工藝段的研究現(xiàn)狀,分析對比了切片、薄化、拋光加工工藝機(jī)理,指出了加工過程中的關(guān)鍵影響因素和未來發(fā)展趨勢。
1、背景與意義
作為半導(dǎo)體產(chǎn)業(yè)中的襯底材料,碳化硅單晶具有優(yōu)異的熱、電性能,在高溫、高頻、大功率、抗輻射集成電子器件領(lǐng)域有著廣泛的應(yīng)用前景。碳化硅襯底加工精度直接影響器件性能,因此外延應(yīng)用對碳化硅晶片表面質(zhì)量的要求極為嚴(yán)苛。碳化硅硬度高、脆性大、化學(xué)性質(zhì)穩(wěn)定,傳統(tǒng)加工方法不完全適用。受加工技術(shù)的制約,目前高表面質(zhì)量碳化硅晶片的加工效率極低。
碳化硅單晶的加工過程主要分為切片、薄化和拋光。全球碳化硅制造加工技術(shù)和產(chǎn)業(yè)尚未成熟,在一定程度上限制了碳化硅器件市場的發(fā)展,要充分實(shí)現(xiàn)碳化硅襯底的優(yōu)異性能,開發(fā)高表面質(zhì)量碳化硅晶片加工技術(shù)是關(guān)鍵所在。本文主要針對碳化硅晶片的加工工藝做相關(guān)論述。
2 碳化硅單晶的切片
作為碳化硅單晶加工過程的第一道工序,切片的性能決定了后續(xù)薄化、拋光的加工水平。切片加工易在晶片表面和亞表面產(chǎn)生裂紋,增加晶片的破片率和制造成本,因此控制晶片表層裂紋損傷,對推動碳化硅器件制造技術(shù)的發(fā)展具有重要意義。
2. 1 切片技術(shù)發(fā)展現(xiàn)狀及趨勢
傳統(tǒng)的鋸切工具如內(nèi)圓鋸片、金剛石帶鋸,轉(zhuǎn)彎半徑受限,切縫較寬,出片率較低,不適用于碳化硅晶體切割。目前報(bào)道的碳化硅切片加工技術(shù)主要包括固結(jié)、游離磨料切片、激光切割、冷分離和電火花切片,不同技術(shù)對應(yīng)的性能指標(biāo)如表 1 所示,其中往復(fù)式金剛石固結(jié)磨料多線切割是最常應(yīng)用于加工碳化硅單晶的方法。
固結(jié)磨料線鋸切片、激光切割、冷分離以及電火花切片等技術(shù)是針對碳化硅材料比較有效的切片方法,原理如圖 1 所示。固結(jié)磨料線鋸切片技術(shù)是指將金剛石磨料固結(jié)在金屬絲上,隨鋸絲運(yùn)動實(shí)現(xiàn)磨粒的鋸切加工,如圖 1( a) 。鋸切區(qū)域磨粒分布均勻,具有效率高、污染小等優(yōu)勢。激光切割技術(shù)則是通過激光處理在內(nèi)部形成改性層從碳化硅晶體上剝離出晶片,該技術(shù)處于研究階段,如圖 1( b) 。冷分離技術(shù)具有材料利用率高,節(jié)能環(huán)保的優(yōu)點(diǎn),如圖 1( c) 。激光在晶錠內(nèi)部形成角質(zhì)層點(diǎn)平面,其上表面涂覆特制的分離材料并冷凍,遇冷收縮可分離晶圓薄片。電火花切片利用脈沖放電對碳化硅單晶進(jìn)行腐蝕切割,精度和生產(chǎn)率高,如圖 1( d) 。加工后碳化硅晶片表面光滑,但切縫較寬,表面損傷層后續(xù)處理工藝需要進(jìn)一步開發(fā)。
2. 2 切片質(zhì)量的主要影響因素與優(yōu)化措施
表層裂紋損傷與切片質(zhì)量密切相關(guān)。4 H-SiC 切片加工可能產(chǎn)生表層裂紋損傷,主要分為亞表面?zhèn)认蛄鸭y損傷和中位裂紋損傷,如圖 2 所示。該裂紋損傷在增加后續(xù)加工成本的同時(shí),容易進(jìn)一步擴(kuò)展導(dǎo)致晶片斷裂。鋸切工藝參數(shù)、固結(jié)磨粒尺寸、工件進(jìn)給運(yùn)動,鋸絲速度控制不當(dāng)都可能導(dǎo)致切片出現(xiàn)表層裂紋損傷。在碳化硅襯底材料上進(jìn)行外延生長、器件制造工藝及器件工作性能都與晶體取向相關(guān)。為了避免方向敏感性導(dǎo)致切片加工時(shí)晶片產(chǎn)生脆性裂紋,在碳化硅晶錠切片前,需要進(jìn)行晶體定向檢測。
碳化硅晶錠一般生長在 SiC{ 0001} 面上,沿平行于晶錠生長方向的 SiC 晶面進(jìn)行切割,可有效降低切片表面貫穿螺型位錯(cuò)密度,提高切片質(zhì)量。切片過程中鋸切工藝參數(shù)的控制對于切片質(zhì)量也至關(guān)重要。減小進(jìn)給量和進(jìn)給力可降低磨粒法向壓應(yīng)力,增大鋸絲速度可降低磨粒切向壓應(yīng)力,小范圍減小鋸絲和鍍層的磨損及磨粒的脫落,但需綜合考慮鋸絲損壞程度與鋸切效率。此外需保持充足均勻的冷卻液以減少殘余熱應(yīng)力,減少鋸絲的振動,避免磨粒應(yīng)力場不穩(wěn)定。
3 碳化硅晶片的薄化
碳化硅斷裂韌性較低,在薄化過程中易開裂,導(dǎo)致碳化硅晶片的減薄非常困難。碳化硅切片的薄化主要通過磨削與研磨實(shí)現(xiàn)。
3. 1 薄化技術(shù)研究現(xiàn)狀
晶片磨削最具代表性的形式是自旋轉(zhuǎn)磨削,晶片自旋轉(zhuǎn)的同時(shí),主軸機(jī)構(gòu)帶動砂輪旋轉(zhuǎn),同時(shí)砂輪向下進(jìn)給,進(jìn)而實(shí)現(xiàn)減薄過程。自旋轉(zhuǎn)磨削雖可有效提高加工效率,但砂輪易隨加工時(shí)間增加而鈍化,使用壽命短且晶片易產(chǎn)生表面與亞表面損傷。加工缺陷的存在嚴(yán)重制約加工精度和效率,為了解決這些問題,研究人員開發(fā)出了不同的輔助技術(shù),如砂輪在線修整,或研制新型軟磨料砂輪,目前主要的技術(shù)包括超聲振動輔助磨削和在線電解修整輔助磨削,加工示意如圖 3。
超聲輔助磨削是通過超聲振動降低磨削力、砂輪磨損量,改善加工質(zhì)量的方法。諸多研究表明,在一定的工藝條件下,相比于普通磨削,超聲輔助磨削更適于硬脆材料的薄化加工。在線電解修整輔助磨削對 4 H-SiC 進(jìn)行薄化加工原理如圖 3( b) 所示。電解作用下,砂輪表面生成絕緣氧化膜,可以減緩砂輪的損耗,同時(shí)承托大量電解脫落的磨粒,與游離磨粒的研磨作用類似,有利于提高磨削表面質(zhì)量。
研磨工藝可分為單面和雙面研磨,小尺寸碳化硅晶片單雙面研磨技術(shù)相繼被開發(fā)。研磨加工碳化硅切片表面時(shí),使用的磨料通常為碳化硼或金剛石,可分為粗磨和精磨。粗磨主要是去除切片造成的刀痕以及切片引起的變質(zhì)層,使用粒徑較大的磨粒。精磨目的是去除粗磨留下的表面損傷層,改善表面粗糙度,使用粒徑較細(xì)的磨粒。
3. 2 影響薄化效果的主要因素及研究趨勢
研究發(fā)現(xiàn),薄化工藝中晶片材料去除率和磨料粒徑大小、密度、研磨盤轉(zhuǎn)速、研磨壓力等因素密切相關(guān)。研磨工藝中需要控制合適的壓力參數(shù),使磨粒具有足夠的機(jī)械能實(shí)現(xiàn)材料去除。研磨壓力和轉(zhuǎn)速過小,則晶片去除率不足,影響加工效率; 若過大,則晶片幾何尺寸變差,且晶片容易被壓碎,影響成品率。研磨液中的磨粒硬度越高粒徑越大,被加工晶片表面粗糙度越大。研磨盤過硬會損壞和污染工件表面,軟研磨盤可允許磨料更多的滑動運(yùn)動,加工后表面光潔度高,但平面度低。未來薄化加工的主要研究方向在于開發(fā)新型砂輪( 主要研究磨料與砂輪結(jié)合劑) 、研磨液/盤( 如半固著磨料磨盤) ,優(yōu)化研磨過程的工藝參數(shù)。此外,研究表明,當(dāng)碳化硅材料去除深度小于 500 nm 時(shí),高壓相變現(xiàn)象會導(dǎo)致碳化硅材料以延性方式去除,延性域模式下的加工損傷深度低于脆性斷裂模式,延性域磨削技術(shù)是薄化工藝的發(fā)展方向之一。為防止碎片,優(yōu)化單面研磨技術(shù)是未來薄化加工大尺寸碳化硅晶片的主要技術(shù)發(fā)展趨勢。
4 碳化硅晶片的拋光
拋光工藝的實(shí)質(zhì)是離散原子的去除。碳化硅單晶襯底要求被加工表面有極低的表面粗糙度,Si面在 0. 3 nm 之內(nèi),C 面在 0. 5 nm 之內(nèi)。根據(jù) GB /T 30656-2014,4 寸碳化硅單晶襯底加工標(biāo)準(zhǔn)如表2 所示。
4. 1 拋光技術(shù)研究現(xiàn)狀
碳化硅晶片的拋光工藝可分為粗拋和精拋,粗拋為機(jī)械拋光,目的在于提高拋光的加工效率。碳化硅單晶襯底機(jī)械拋光的關(guān)鍵研究方向在于優(yōu)化工藝參數(shù),改善晶片表面粗糙度,提高材料去除率。
目前,關(guān)于碳化硅晶片雙面拋光的報(bào)道較少,相關(guān)工藝參數(shù)有待進(jìn)一步優(yōu)化。精拋為單面拋光,化學(xué)機(jī)械拋光是應(yīng)用最為廣泛的拋光技術(shù),通過化學(xué)腐蝕和機(jī)械磨損協(xié)同作用,實(shí)現(xiàn)材料表面去除及平坦化。晶片在拋光液的作用下發(fā)生氧化反應(yīng),生成的軟化層在磨粒機(jī)械作用下相對容易被除去。作為單晶襯底加工的最后一道工藝,化學(xué)機(jī)械拋光是實(shí)現(xiàn)碳化硅襯底全局平坦化的常用方法,也是保證被加工表面實(shí)現(xiàn)超光滑、無缺陷損傷的關(guān)鍵工藝。目前報(bào)道的典型精拋工藝技術(shù)對比如表 3 所示。
碳化硅單晶的精拋工藝主要研究方向是開發(fā)結(jié)合化學(xué)和機(jī)械兩方面增效的復(fù)合工藝,化學(xué)增效方法主要有電化學(xué)、磁流變、等離子體、光催化等,機(jī)械增效方法主要有超聲輔助、混合磨粒和固結(jié)磨粒拋光等方法,相關(guān)加工原理如圖 4 所示。
4. 2 影響 CMP 的關(guān)鍵因素與發(fā)展趨勢
CMP 的機(jī)械和化學(xué)作用達(dá)平衡時(shí),拋光效果可達(dá)最優(yōu)。CMP 的拋光效果主要受工藝參數(shù)、拋光液、拋光墊三方面參數(shù)的影響。拋光液和拋光墊是 CMP 的主要耗材,控制優(yōu)化其性能以保證可重復(fù)的拋光效率對于工藝穩(wěn)定性至關(guān)重要。對拋光液進(jìn)行改良,研發(fā)具備自催化作用的拋光墊,是未來CMP 耗材的研究方向。上述新型拋光方法中如 PAP、CMRF 需要大功率高溫裝置,系統(tǒng)成本高,工藝可操作性差,目前主流的碳化硅晶片精拋工藝仍是 CMP。碳化硅 CMP 過程材料去除率模型的建立以及催化、電化學(xué)增效機(jī)理亟待進(jìn)一步研究。綜合利用碳化硅氧化理論及催化化學(xué)等方法,將多種化學(xué)和機(jī)械增效技術(shù)進(jìn)行復(fù)合,如超聲輔助電化學(xué)機(jī)械拋光、磁流變-催化復(fù)合輔助拋光、固結(jié)磨粒-超聲-催化拋光技術(shù)等,以同時(shí)提高碳化硅表層氧化速率與氧化層機(jī)械去除速率,是未來優(yōu)化碳化硅拋光工藝效率和質(zhì)量的發(fā)展方向。
5 討論
碳化硅晶片加工是單晶生長后的一大高難度工藝,國內(nèi)相關(guān)單位現(xiàn)已能夠加工出基本滿足器件制備要求的襯底片,但晶片表面加工精度與國外相比仍然有較大差距,國外對相關(guān)理論和工藝都存在技術(shù)封鎖,研究人員需要采用更先進(jìn)的精密工藝設(shè)備,進(jìn)一步研究切片、薄化、拋光過程中的機(jī)理,優(yōu)化晶片加工方法,制備出高質(zhì)量的碳化硅襯底。
來源:張璽, 王蓉, 張序清, 楊德仁, 皮孝東
審核編輯:郭婷
-
半導(dǎo)體
+關(guān)注
關(guān)注
334文章
27286瀏覽量
218062 -
碳化硅
+關(guān)注
關(guān)注
25文章
2748瀏覽量
49017
原文標(biāo)題:碳化硅單晶襯底加工技術(shù)現(xiàn)狀及發(fā)展趨勢綜述——浙大科創(chuàng)中心先進(jìn)半導(dǎo)體研究院
文章出處:【微信號:第三代半導(dǎo)體產(chǎn)業(yè),微信公眾號:第三代半導(dǎo)體產(chǎn)業(yè)】歡迎添加關(guān)注!文章轉(zhuǎn)載請注明出處。
發(fā)布評論請先 登錄
相關(guān)推薦
研究碳化硅襯底和外延的實(shí)驗(yàn)報(bào)告
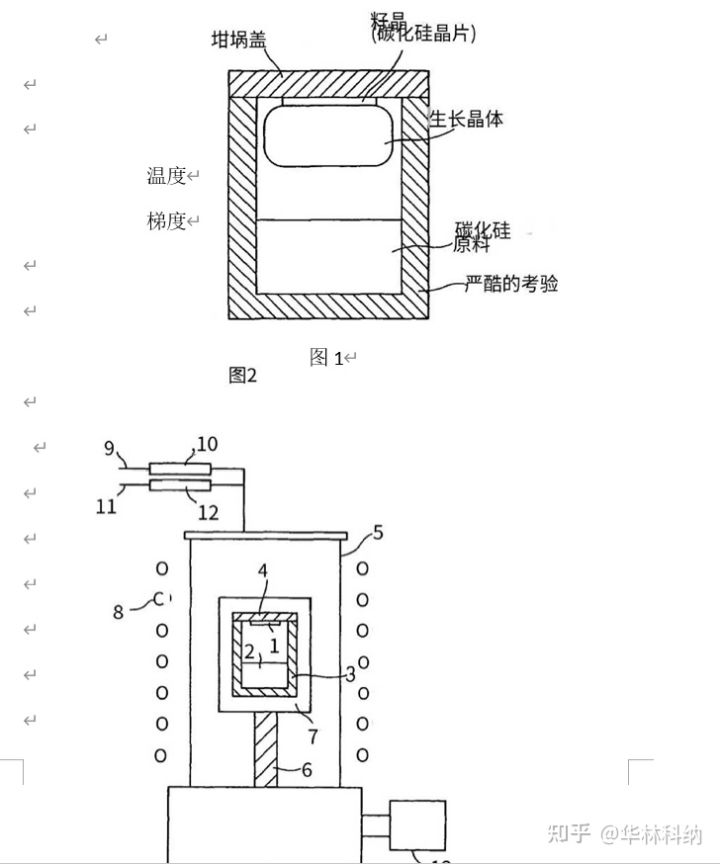
簡述LED襯底技術(shù)
表面硅MEMS加工技術(shù)的關(guān)鍵工藝
碳化硅深層的特性
請教碳化硅刻蝕工藝
歸納碳化硅功率器件封裝的關(guān)鍵技術(shù)
碳化硅單晶體二極管的優(yōu)勢及應(yīng)用范圍
同光晶體完成融資,將用于6英寸碳化硅襯底項(xiàng)目
碳化硅單晶襯底加工技術(shù)現(xiàn)狀及發(fā)展趨勢
碳化硅行業(yè)現(xiàn)狀及前景怎么樣
SiC碳化硅二極管和SiC碳化硅MOSFET產(chǎn)業(yè)鏈介紹
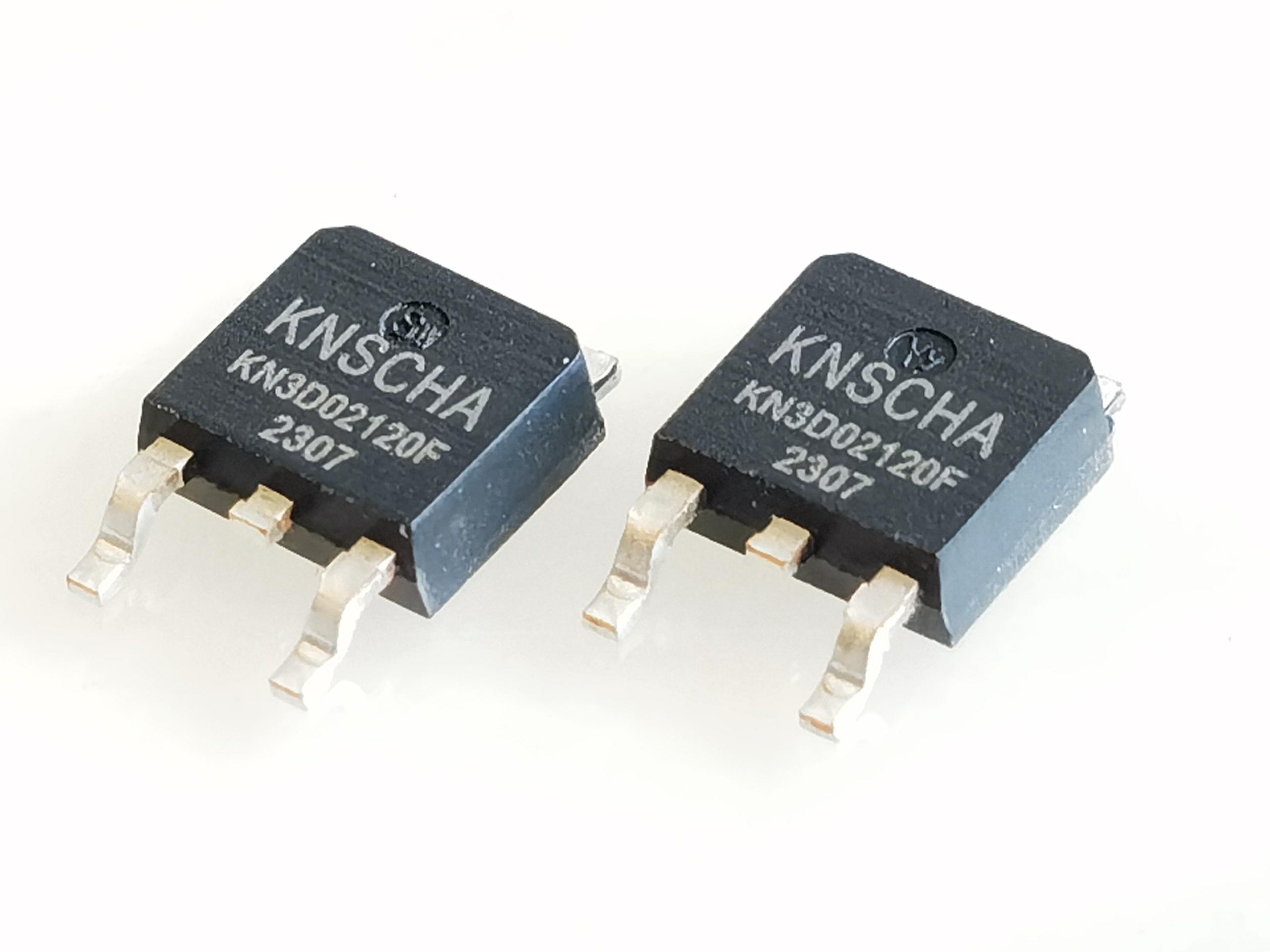
簡述碳化硅襯底類型及應(yīng)用
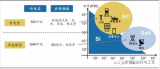
SiC碳化硅單晶的生長原理
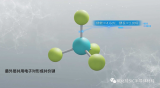
國內(nèi)碳化硅襯底生產(chǎn)企業(yè)盤點(diǎn)
碳化硅單晶襯底的常用檢測技術(shù)
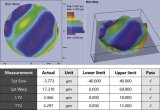
評論