現(xiàn)代LTCC技術是將低溫燒結陶瓷粉制成厚度精確而且致密的生瓷帶,在生瓷帶上利用激光打孔、微孔注漿和精密導體漿料印刷等工藝制出所設計的電路版圖,并將多個元器件埋入多層陶瓷基板中,然后疊壓在一起,內外電極可選用Ag、Cu和Au等金屬材料,在小于1000℃的溫度條件下燒結,最終制成3D的高密度集成電路,也可制成內置無源元件的3D電路基板,也可以在其表面貼裝IC和有源器件制成無源/有源集成的功能模塊。
目前來看,LTCC技術是解決電子產(chǎn)品“90%問題”的主流技術,是實現(xiàn)電子整機或系統(tǒng)小型化、高性能化與高密度化的首選方案,被廣泛應用于射頻電路系統(tǒng)。
但LTCC多層電路基板制造工藝流程較長,工藝復雜,基板收縮率、翹曲度、層間對位精度等都是影響產(chǎn)品性能的重要因素。本文將根據(jù)上述技術難點,對如何優(yōu)化工藝參數(shù)及解決上述問題展開論述分析。
三大影響因素分析
① 收縮率偏差
LTCC收縮率與其密度有直接關系,密度越大收縮率越小,密度越小收縮率越大,反應到工藝參數(shù)上來,密度與層壓壓力相對應,因此可以通過調控層壓壓力來改變LTCC產(chǎn)品的收縮率,使之達到設計要求。
且LTCC基板由于存在金屬通孔、印刷金屬導線,這些金屬的收縮率不同于白瓷收縮率,因此相同層壓壓力下LTCC產(chǎn)品的收縮率與白瓷的收縮率有一定差異,需要進一步研究其規(guī)律,積累工藝數(shù)據(jù),進行層壓壓力相應的調整。
② 基板翹曲
● 燒結原因:燒結工藝與基板翹曲度、收縮率有直接關系,LTCC基板的燒結過程實際是一個放熱吸熱反應的過程。排膠階段(室溫至500℃左右)基板中有機物分解揮發(fā),質量減輕;燒結階段(700℃~850℃左右)基板發(fā)生結晶和析晶反應,伴隨反應的進行,基板收縮。因此低溫階段、高溫階段的燒結時間,升溫速率與基板收縮程度、翹曲程度關系密切,需要優(yōu)化燒結曲線,通過試驗調整排膠階段升溫速率、時間,燒結階段升溫速率、時間,各階段空氣流量等重要工藝參數(shù)。
● 基板結構及金屬分布問題:LTCC基板的結構也是決定LTCC基板燒結翹曲度的關鍵因素,當LTCC基板上存在多種規(guī)格的空腔結構時,其結構難以均衡對稱,同時由于LTCC基板上含有大量通孔及密集金屬導線,這些都難以均勻分布,這樣就容易導致其翹曲度超差。
● 漿料選用問題:不同銀漿、金漿與生瓷帶熱膨脹系數(shù)匹配性不同,因此大面積印刷層選用不同漿料時對基板翹曲度的影響尤為明顯。
③ 通孔層間對位偏差
LTCC基板層間對位偏差與打孔精度、生瓷片自身收縮情況、各層印刷導體情況,疊層對位精度等眾多因素相關,是控制的難點,因此需要對整個工藝流程進行監(jiān)控,找出主要影響因素,進行優(yōu)化控制。按照帶膜工藝流程進行LTCC制造,對全過程進行錯位監(jiān)控。
帶膜工藝LTCC通孔錯位原因分析表(單位:μm)
通過全流程跟蹤監(jiān)測,帶膜生瓷片在撕膜后會有一個應力的釋放,導致較大變形,其中主要形變方向為生瓷流延方向,表現(xiàn)為放大,范圍約為40μm~70μm,垂直于流延方向則表現(xiàn)為收縮,范圍約為10μm~20μm,是帶膜工藝通孔錯位的主要原因。
工藝方案及試驗結果
① 收縮率偏差控制工藝方案
為了尋求實際收縮率與曲線上收縮率的誤差,通過多輪的層壓試驗,實測LTCC收縮率與LTCC“層壓壓力-密度-收縮率”關系曲線上收縮率誤差約為0.2%~0.3%,依此指導實際生產(chǎn)。在LTCC制造中,工藝設計收縮率15.8%,為達到次收縮率,因為上述試驗證明實測LTCC收縮率與曲線上收縮率誤差約為0.2%~0.3%,因此要到達15.8%的收縮率,應選用16%收縮率所對應的層壓壓力,即力3000psi。實際效果表明效果較好,達到了設計收縮率。
② 基板翹曲度控制工藝方案
● 燒結工藝優(yōu)化:降低排膠階段升溫速率,優(yōu)化各階段氣流量,緩解不同材料熱膨脹系數(shù)不匹配的應力。
● 布版設計優(yōu)化:對于單塊基板內部無法滿足金屬化平衡分布的情況,擬在版圖布局時進行對稱性布局,使其在整版中形成金屬化平衡分布,燒結時再進行整版燒結,這樣就可以有效地改善基板平整度。
單塊LTCC的孔分布及金屬導線分布的不對稱性
● 漿料選用優(yōu)化:在混合漿料體系中,大面積底層盡量選用同種材質的漿料,對于LTCC背面焊接層,確需選擇不同漿料時,可盡量選擇后燒型漿料,以此可降低燒結難度,改善基板翹曲度。
按照上述方案進行工藝優(yōu)化后,將生產(chǎn)的LTCC基板進行了基板外形尺寸及翹曲度測試,結果表明,通過上述改進后,基板外形尺寸精度及翹曲度指標完全滿足工藝要求,改進效果明顯,基板本身及空腔底面平整度均達到了較好效果,基板均達到小于2‰的翹曲度。
③ 通孔層間對位偏差控制
帶膜工藝,在疊片前撕膜,生瓷片在流延時積累的應力在撕膜時集中釋放,造成生瓷片無規(guī)律性變形,引起生瓷片上通孔及導線位置偏移。改為無膜工藝,在打孔前對生瓷片進行撕膜、自然放置老化處理,以釋放應力。
無膜工藝流程
通過上述分析可知,生瓷片脫膜后通過老化工序,加速生瓷片老化釋放壓力,減小生瓷片在其后加工過程中的形變量,然后再進行生瓷片加工,從而有效地改善了LTCC基板層間對位偏差,因此老化效果將對后續(xù)LTCC基板層間對位偏差有重要影響,老化不充分,脫膜生瓷片在后續(xù)加工中仍將有較大形變,為此需要對老化工藝開展研究,較好的老化的方法通常是對生瓷片脫膜后進行常溫下自然晾置,其關鍵工藝參數(shù)時晾置時間。
無膜生瓷片老化工藝實驗(單位:mm)
試驗方法是在脫膜后的生瓷片上沖孔,通過測量X、Y方向通孔間距以判斷生瓷片是否老化充分了。試驗表明,生瓷片脫膜后自然晾置24h后老化充分,后續(xù)生瓷片形變量不大,因此無膜工藝老化時間可設置為自然晾置不低于24h即可。無膜工藝流程下打孔后至疊片前,打孔、填孔、印刷、漿料干燥等工序操作造成的生瓷片形變約在+15μm左右,完全滿足工藝要求,該工藝流程下填孔層間對位偏差將得以改善。采用上述方案后,通孔對位精度明顯提高,達到≤40μm水平。
結 論
綜上可知,實際LTCC基板由于存在金屬通孔、印刷金屬導線,這些金屬的收縮率不同于白瓷收縮率,因此相同層壓壓力下LTCC產(chǎn)品的收縮率與白瓷的收縮率有一定差異,可通過積累工藝數(shù)據(jù),進行層壓壓力相應的調整來解決收縮率偏差問題。對于LTCC基板燒結收縮率,其不僅與燒結工藝有關,還與基板對稱性設計、電路布局、漿料選用關系密切;帶膜工藝較無膜工藝在通孔層間對位精度控制上難度更大,撕膜時應力釋放是導致層間通孔對位偏差的主要原因,無膜工藝更適合層間對位精度要求較高的應用。
審核編輯:湯梓紅
-
工藝
+關注
關注
4文章
592瀏覽量
28779 -
制造工藝
+關注
關注
2文章
179瀏覽量
19751 -
基板
+關注
關注
2文章
274瀏覽量
23003 -
LTCC
+關注
關注
28文章
127瀏覽量
48778 -
有源器件
+關注
關注
0文章
82瀏覽量
14730
原文標題:LTCC基板三大關鍵工藝問題的優(yōu)化方案
文章出處:【微信號:中科聚智,微信公眾號:中科聚智】歡迎添加關注!文章轉載請注明出處。
發(fā)布評論請先 登錄
相關推薦
層壓板與LTCC板射頻模塊的比較
LTCC電子器件的模塊化
基于LTCC技術實現(xiàn)SIP的優(yōu)勢和特點討論
LTCC技術有什么特點?
LTCC多層濾波器的工藝怎么實現(xiàn)?
LTCC技術是什么?應用LTCC的優(yōu)勢是什么?
LTCC多層微波傳輸線的性能優(yōu)化
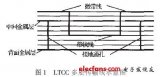
LTCC多層互連基板工藝及優(yōu)化

LTCC基板密集孔區(qū)域研究
LTCC基板關鍵工藝問題解決方案
LTCC通孔漿料的工藝研究
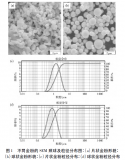
大尺寸LTCC基板高釬透率焊接工藝研究
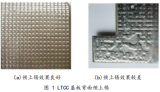
評論