共讀好書
蓋曉晨
摘要:
在航空航天領(lǐng)域中,金屬封裝材料被廣泛應(yīng)用,對(duì)其加工制造工藝的研究具有重要的意義。近年來,金屬基復(fù)合材料逐漸代替?zhèn)鹘y(tǒng)金屬材料應(yīng)用于新一代的航空航天電子封裝領(lǐng)域中,對(duì)金屬基復(fù)合材料的加工工藝進(jìn)行優(yōu)化,是滿足新一代電子封裝產(chǎn)品需求的關(guān)鍵。對(duì)傳統(tǒng)封裝金屬和金屬基復(fù)合封裝材料加工制造的研究及應(yīng)用現(xiàn)狀進(jìn)行闡述,分析金屬基復(fù)合封裝材料的加工難點(diǎn),并對(duì)該領(lǐng)域未來的發(fā)展進(jìn)行展望。
1 序言
在航空航天領(lǐng)域中,電子封裝產(chǎn)品需具有氣密性好、不受外界環(huán)境因素的影響、可靠性高等特點(diǎn)。由于在各種形式的封裝中,以微波組件為主的金屬封裝產(chǎn)品具有上述特性,因此在航空航天領(lǐng)域中,金屬基封裝材料被大量使用。近年來,由于封裝材料向高導(dǎo)熱、高強(qiáng)度、低密度的方向發(fā)展,金屬封裝材料由合金向金屬基復(fù)合材料的方向發(fā)展,因此金屬封裝材料的加工難度也隨之增加。為了滿足封裝組件結(jié)構(gòu)復(fù)雜、高精度等要求,對(duì)電子封裝用金屬基復(fù)合材料加工制造工藝的研究具有至關(guān)重要的意義。
本文對(duì)傳統(tǒng)金屬封裝材料和金屬基復(fù)合封裝材料的加工制造現(xiàn)狀進(jìn)行闡述,總結(jié)電子封裝用金屬基復(fù)合材料切削加工的研究成果,并分析目前仍存在的難點(diǎn),為后續(xù)電子封裝用金屬基復(fù)合材料的加工制造的發(fā)展提供參考。
2 電子封裝用金屬及其復(fù)合材料簡介
傳統(tǒng)的封裝金屬材料有鋁合金、銅合金、鋼及可伐合金等,其性能見表1。理想的封裝材料必須滿足以下基本要求:與芯片材料和基板材料相匹配的熱膨脹系數(shù)(3×10 -6 /K~7×10 -6 /K),高的熱導(dǎo)率,綜合的力學(xué)性能以及低密度 [1] ??梢妭鹘y(tǒng)封裝金屬材料均存在熱導(dǎo)率、熱膨脹系數(shù)等不理想問題。
隨著航空航天的電子裝備向高功率、高密度、小型化、輕量化及高可靠性的方向發(fā)展,對(duì)封裝材料的性能也提出了更高的要求,傳統(tǒng)的單一金屬封裝材料已難以滿足電子封裝的綜合性能需求。如將金屬材料與其他材料復(fù)合,則材料性能大大提升,因此金屬基復(fù)合材料得到越來越廣泛的應(yīng)用。金屬基復(fù)合材料有很多種,作為封裝的主要有銅基復(fù)合材料和鋁基復(fù)合材料,目前應(yīng)用較廣泛的有高硅鋁合金(SiC/Al復(fù)合材料)和金剛石/銅、金剛石/鋁等金屬基金剛石復(fù)合材料。金屬基復(fù)合封裝材料的性能見表2??梢娖浞庋b性能較傳統(tǒng)金屬封裝材料有極大提升。
3 傳統(tǒng)金屬封裝材料加工制造的現(xiàn)狀
微波組件腔體的特點(diǎn)為結(jié)構(gòu)復(fù)雜、精度較高、螺紋和小孔數(shù)量較多及毛刺要求嚴(yán)格等。傳統(tǒng)的電子封裝金屬材料有鋁合金、銅合金和可伐合金等,其中鋁合金和銅合金為易加工材料,加工難度小,加工工藝成熟穩(wěn)定;可伐合金硬度較高、耐磨、不易切削,雖有加工難度,但加工工藝也較為成熟。
針對(duì)加工難度較大的可伐合金,首先應(yīng)提升刀具耐磨性,如使用硬質(zhì)合金涂層刀具;避免在工件上垂直下刀,加工外形時(shí)側(cè)面進(jìn)刀,加工內(nèi)腔時(shí)折線進(jìn)刀或螺旋進(jìn)刀以減小刀具磨損;使用在線刀具測量系統(tǒng)保證及時(shí)換刀。其次減少加工過程中的刀具振動(dòng),避免對(duì)零件精度造成影響,如裝夾時(shí)盡量縮短刀具的懸伸量;因微波腔體內(nèi)圓角較小,加工內(nèi)圓角時(shí)需降低進(jìn)給速度,避免因刀具直徑小而發(fā)生振顫。此外,可采用超聲振動(dòng)等輔助手段提升切削精度和表面質(zhì)量 [2] 。
4 硅鋁合金加工制造的研究現(xiàn)狀
隨著新一代的航空航天電子裝備對(duì)產(chǎn)品輕量化、高功能密度等要求越來越高,硅鋁合金在航空航天微波組件中的應(yīng)用越來越廣泛。但其加工工藝尚未像傳統(tǒng)金屬封裝材料一樣成熟,只有部分技術(shù)能力較強(qiáng)的企業(yè)具有穩(wěn)定加工的能力。硅鋁合金因其成分、微觀結(jié)構(gòu)等原因,材料脆性較高。
硅鋁合金加工難點(diǎn)如下:加工過程中材料易崩邊、有裂紋,尤其在棱邊、棱角、通孔底部等部位易發(fā)生脆斷;刀具磨損嚴(yán)重,加工效率低;螺紋加工難度大,絲錐易斷裂。
因此解決上述難點(diǎn)是硅鋁合金切削加工的關(guān)鍵技術(shù),加工關(guān)鍵點(diǎn)如下。
(1)刀具的選用及使用針對(duì)硅鋁合金復(fù)合材料的高脆性特點(diǎn),選擇銑削刀具時(shí)應(yīng)考慮刀具的耐磨性、硬度及導(dǎo)熱性,其中耐磨性最為重要。因此涂層刀具、PCD刀具適用于硅鋁合金的加工。
在實(shí)際加工中,需根據(jù)加工成本和加工效果,綜合分析確定銑削刀具,由于PCD刀具使用成本較高,限制了其廣泛使用,因此涂層刀具在硅鋁合金的加工中應(yīng)用最為廣泛。近年來學(xué)者對(duì)不同涂層的刀具切削硅鋁合金展開了研究。LIANG等采用PCD、納米金剛石涂層和K68硬質(zhì)合金刀具對(duì)A390硅鋁合金進(jìn)行切削試驗(yàn),結(jié)果表明,納米金剛石涂層刀具的耐磨性與PCD相當(dāng),且其加工的工件表面粗糙度等于或優(yōu)于PCD刀具 [3] 。湖南科技大學(xué)的張深圳等人總結(jié)了各種改善涂層沉積工藝的刀具的性能,得出MCD/NCD和無氫DLC涂層刀具在高溫下?lián)碛懈哂捕?、低摩擦因?shù)等特點(diǎn),在切削硅鋁合金時(shí)表現(xiàn)出優(yōu)異的性能,被認(rèn)為是最有潛力提高硅鋁合金可加工性的刀具 [4] 。
(2)切削參數(shù)的設(shè)計(jì)切削加工參數(shù)對(duì)加工表面質(zhì)量具有直接影響,硅鋁合金這類新型金屬合金材料,對(duì)其切削加工參數(shù)進(jìn)行研究意義重大。南京航空航天大學(xué)的程磊等人通過正交銑削試驗(yàn)并采用響應(yīng)曲面法建立刀具壽命、表面粗糙度、切削力模型,分別得出最低成本和最高加工效率下的加工參數(shù) [5] 。西華大學(xué)的余宗寧等人,以正交試驗(yàn)法為基礎(chǔ),通過有限元仿真軟件對(duì)TiAlN涂層銑刀銑削CE11高硅鋁合金的過程進(jìn)行虛擬仿真分析,并通過試驗(yàn)驗(yàn)證主軸轉(zhuǎn)速n=1800r/min,每齒進(jìn)給量f z =0.08mm/z,銑削寬度a e =2mm,背吃刀量a p =2mm為獲得最優(yōu)表面粗糙度的工藝參數(shù) [6] 。ZHOU等通過有限元仿真模型優(yōu)化參數(shù)并通過試驗(yàn)驗(yàn)證,得出PCD刀具切削ZL109硅鋁合金的最佳切削參數(shù)為:切削速度v=320m/min,背吃刀量a p =0.1mm,進(jìn)給量f=0.1mm/r [7] 。
(3)加工工藝的優(yōu)化合理規(guī)劃切削路徑、改進(jìn)切削方法、利用輔助手段等加工工藝的優(yōu)化也是獲得高質(zhì)量零件的重要因素。為避免加工中在棱角處產(chǎn)生崩邊,我公司高鍵等研究了崩邊產(chǎn)生的機(jī)理,分析出切削加工的進(jìn)刀和出刀階段是導(dǎo)致出現(xiàn)崩邊的關(guān)鍵階段,得出在設(shè)計(jì)切削路徑時(shí)應(yīng)盡量避免刀具側(cè)刃與工件的接觸,而應(yīng)多采用刀具底刃與工件接觸的方式的結(jié)論 [8] 。SUN等提出正反向精加工與分步進(jìn)給切削加工的方法(見圖1),并通過試驗(yàn)表明分步進(jìn)給切削加工和正反向精加工與普通切削加工相比表面質(zhì)量更高 [9]。BAI等采用超聲輔助對(duì)硅鋁合金進(jìn)行了車削加工,超聲輔助改變了刀具和材料中硬質(zhì)顆粒的相互作用,降低了硬質(zhì)顆粒在工件表面的犁削作用,減少了表面劃痕缺陷 [10] 。
(4)螺紋加工的設(shè)計(jì)微波組件通常需加工螺紋,且螺紋規(guī)格較小,一般為M1.6~M3。針對(duì)硅鋁合金高脆性及粉末狀切屑的特點(diǎn),加工螺紋易發(fā)生絲錐斷裂、爛牙、螺紋有裂紋等缺陷,目前硅鋁合金螺紋加工仍主要以鉗工手工加工為主,效率較低。因此,研究在機(jī)床上實(shí)現(xiàn)螺紋的高質(zhì)量、高穩(wěn)定性加工,對(duì)提升加工效率具有重要意義。BHOWMICK進(jìn)行硅鋁合金的攻螺紋試驗(yàn),分析出在高速切削條件下,切削溫度高導(dǎo)致鋁基體的軟化,致使刀具表面產(chǎn)生粘結(jié)而失效 [11] 。電子科技大學(xué)的文磊通過硬質(zhì)合金涂層鉆頭和絲錐對(duì)硅鋁合金的螺紋加工展開研究,得出M1.6~M3螺紋加工的推薦工藝參數(shù)[12] 。
綜上所述,硅鋁合金的切削加工取得了一定的研究成果,但尚未形成成熟的應(yīng)用,因其難加工的特性,與傳統(tǒng)金屬材料相比,距離形成普遍、穩(wěn)定的加工能力仍有一段距離。未來,針對(duì)刀具尤其是絲錐,優(yōu)化制備工藝,提升刀具的耐磨性,以及開發(fā)新型超硬材料刀具,仍是關(guān)鍵。另外,需繼續(xù)深入運(yùn)用有限元仿真技術(shù),針對(duì)硅鋁合金切削加工的仿真建模,開發(fā)更精準(zhǔn)的仿真模型,對(duì)各項(xiàng)工藝參數(shù)進(jìn)行進(jìn)一步的優(yōu)化,提升加工的質(zhì)量和效率,力爭攻克機(jī)床加工螺紋的難點(diǎn)。
5 金屬基金剛石的生產(chǎn)制造研究現(xiàn)狀
隨著航空航天電子裝備的持續(xù)換代提升,設(shè)備功率也持續(xù)加大,散熱問題早已成為制約航空航天領(lǐng)域電子封裝發(fā)展的重要因素。金剛石/銅、金剛石/鋁等金屬基金剛石復(fù)合材料因其高熱導(dǎo)率、膨脹系數(shù)可控等優(yōu)異的性能,在電子封裝領(lǐng)域是極具前景的材料。目前金屬基金剛石的制備方法有粉末冶金法、高溫高壓法、熔體浸滲法以及放電等離子燒結(jié)法等。金剛石和銅、鋁的接觸界面結(jié)合狀況較差,在界面之間熱阻較高,材料制備的關(guān)鍵是改善金剛石和銅、鋁之間的界面問題,因此需要通過技術(shù)手段對(duì)兩者界面進(jìn)行改性,提升相互之間的浸潤性。目前主要的界面改性手段有金剛石表面改性處理和金屬基體的合金化處理 [13] 。
金屬基金剛石因金剛石硬度較高而導(dǎo)致其后續(xù)加工困難,江南大學(xué)的胡熠聞對(duì)鋁基金剛石的切削可行性進(jìn)行了研究,得出大粒徑鋁基金剛石無法進(jìn)行有效切削,小粒徑、金剛石體積分?jǐn)?shù)低的鋁基金剛石在切削量不大的情況下,具備一定的切削性能;但小粒徑、低體積分?jǐn)?shù)的鋁基金剛石導(dǎo)熱性能有所下降,因此作者提出了一種3層式金剛石/鋁的結(jié)構(gòu),中間為大粒徑、高體積分?jǐn)?shù)的金剛石/鋁,上下表面的切削區(qū)域?yàn)樾×?、低體積分?jǐn)?shù)的金剛石/鋁,如圖2、圖3所示,保證熱性能的同時(shí)使材料具備一定的可加工性 [14] 。
目前投入使用的金屬基金剛石產(chǎn)品的結(jié)構(gòu)通過材料成形直接實(shí)現(xiàn),產(chǎn)品形狀簡單、尺寸有限且成本高昂 [15] 。為了滿足電子封裝的要求,需開發(fā)結(jié)構(gòu)復(fù)雜、尺寸范圍更廣或具備可加工性的金屬基金剛石復(fù)合材料。因此,降低制造成本、產(chǎn)品結(jié)構(gòu)尺寸多樣化和提升材料加工性能是今后的研究方向。
6 結(jié)束語
結(jié)合目前國內(nèi)外關(guān)于金屬基封裝材料加工制造的研究和應(yīng)用進(jìn)展,以及航空航天領(lǐng)域?qū)﹄娮臃庋b產(chǎn)品的需求,對(duì)今后的發(fā)展進(jìn)行如下展望。
1)針對(duì)硅鋁合金,應(yīng)利用有限元技術(shù),建立更深入、準(zhǔn)確的切削仿真模型,為螺紋加工等各個(gè)難加工過程的刀具結(jié)構(gòu)和工藝參數(shù)的優(yōu)化提供理論支撐;進(jìn)一步優(yōu)化加工工藝,并改進(jìn)加工工具,尤其是絲錐;開發(fā)新型超硬材料刀具、新的涂層材料及優(yōu)化涂層工藝也是重要的研究方向。
2)針對(duì)金屬基金剛石復(fù)合材料,需繼續(xù)改進(jìn)界面改善手段,提升材料的熱學(xué)性能;對(duì)金屬基金剛石復(fù)合材料的制備工藝進(jìn)行改進(jìn)和開發(fā),獲得更復(fù)雜、更廣尺寸范圍的產(chǎn)品結(jié)構(gòu)以滿足電子封裝的結(jié)構(gòu)需求,以及實(shí)現(xiàn)產(chǎn)品的可加工性,需在后續(xù)的研究中重點(diǎn)關(guān)注。
審核編輯 黃宇
-
電子封裝
+關(guān)注
關(guān)注
0文章
74瀏覽量
10861
發(fā)布評(píng)論請(qǐng)先 登錄
相關(guān)推薦
復(fù)合材料的機(jī)械性能測試詳解
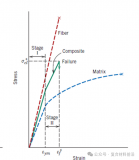
高導(dǎo)電石墨烯增強(qiáng)銅基復(fù)合材料的研究進(jìn)展
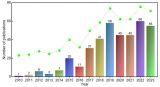
復(fù)合材料的測試及分析指南
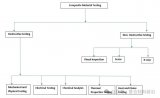
C/C復(fù)合材料連接技術(shù)研究進(jìn)展
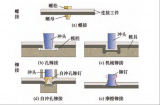
粉末涂料在復(fù)合材料部件上的應(yīng)用
石墨烯化學(xué)鍍銅對(duì)放電等離子燒結(jié)石墨烯增強(qiáng)鋁基復(fù)合材料組織和性能的影響
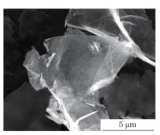
碳/碳復(fù)合材料的優(yōu)點(diǎn)有哪些
IC 封裝載板用有機(jī)復(fù)合基板材料研究進(jìn)展
高絕緣散熱材料 | 石墨片氮化硼散熱膜復(fù)合材料
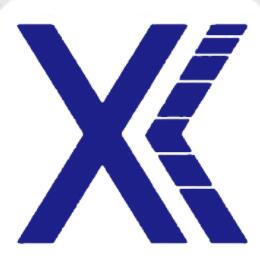
射頻功率放大器在紡織復(fù)合材料研究中的應(yīng)用
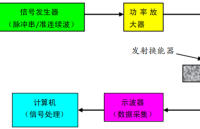
搪瓷釜脫瓷嚴(yán)重漏介質(zhì),用高分子復(fù)合材料輕松修補(bǔ)
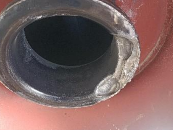
用于制造紫外超構(gòu)表面的定制化高折射率納米復(fù)合材料
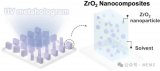
電子封裝用金屬基復(fù)合材料加工制造的研究進(jìn)展
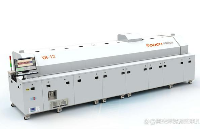
評(píng)論