電路板在生產(chǎn)過程中可焊性差,有時候還會產(chǎn)生PCB焊盤脫落的現(xiàn)象,我們可能會直接想到是由于PCB電路板焊接加工的問題,但事實上原因并沒有這么簡單,接下來就對PCB焊盤脫落原因進行分析。
首先PCB板材與阻焊膜不匹配,熱風(fēng)整平時過錫次數(shù)太多,錫液溫度或預(yù)熱溫度過高,焊接時次數(shù)過多等等都會導(dǎo)致PCB焊盤脫落溫度過高。一般的雙面板或單面板比較容易焊盤脫落,多層板有大面積的鋪地,散熱快,焊接時需要的溫度也高,也沒那么容易脫落。
PCB焊接掉焊盤的原因:
1:反復(fù)焊接一個點會把焊盤焊掉;
2:烙鐵溫度太高容易把焊盤焊掉;
3:烙鐵頭給焊盤施加的壓力過大且焊接時間過長會把焊盤焊掉;脫落的原因分析:線路板使用過程中,經(jīng)常出現(xiàn)焊盤脫落,尤其是在線路板返修的時候,在使用電烙鐵時,非常容易出現(xiàn)焊盤脫落的現(xiàn)象 ,在本文中對焊盤脫落的原因進行一些分析,也針對原因采取相應(yīng)的對策。針對焊盤在使用條件下容易脫落,采取如下幾個方面,盡可能的提高線路板焊盤耐焊接次數(shù),以滿足客戶的需求。為改善PCBA焊盤的可焊性,防止焊盤脫落,改善焊接工藝,提高員工的焊接水平。
覆銅板選用正品有品質(zhì)保證的廠家出品的基材。一般正品覆銅板的玻璃纖維布選材和壓合工藝能保證制造出得線路板 耐焊性符合客戶使用要求。線路板出廠前用真空包裝,放置干燥劑,保持線路板始終在干燥的狀態(tài)。
為減少虛焊,提高可焊性創(chuàng)造條件。針對電烙鐵返修時對焊盤的熱沖擊,我們盡可能通過電鍍的增加焊盤銅箔的厚度,這樣當電烙鐵給焊盤加熱時,銅箔 厚德焊盤導(dǎo)熱性明顯增強,有效的降低的焊盤的局部高溫,同時,導(dǎo)熱快使焊盤更容易拆卸。達到焊盤的耐焊性。
-
pcb
+關(guān)注
關(guān)注
4319文章
23080瀏覽量
397496 -
電路板
+關(guān)注
關(guān)注
140文章
4951瀏覽量
97689 -
焊盤
+關(guān)注
關(guān)注
6文章
551瀏覽量
38134
發(fā)布評論請先 登錄
相關(guān)推薦
回流焊溫度對電路板的影響及關(guān)系分析

PCM2707按照datasheet參考電路2焊的電路板,在win7下無法識別,是什么原因?
深度揭秘造成插件電感引腳脫落的可能原因
焊盤與焊盤的距離規(guī)則怎么設(shè)置
焊盤通孔尺寸怎么確定的
pcb焊盤直徑怎么設(shè)置
pcb焊盤區(qū)域凸起可以焊嗎
pcb怎么改變焊盤大小
pcb設(shè)計中焊盤的形狀和尺寸是什么
電路板檢修用什么檔位好
電路板測試步驟有哪些 電路板測試儀器有哪些
Xilinx FPGA BGA設(shè)計:NSMD和SMD焊盤的區(qū)別
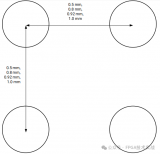
評論