某純電動三合一電驅(qū)動總成在整車節(jié)氣門全開(Wide Open Throttle, WOT)、脈沖序列輸出(Pulse Train Output, POT)加速和反拖滑行行駛工況時(shí),在車外和車內(nèi)近場都出現(xiàn)明顯異響、嘯叫等噪音,主要發(fā)生頻率范圍大概在20~5 000 Hz,很容易被人耳朵識別??刂茋[叫NVH問題的途徑如圖1所示,其中控制嘯叫的兩個(gè)主要途徑是控制激勵源和傳播路徑,本文主要是通過控制激勵源來優(yōu)化NVH問題達(dá)到目的。
圖1 控制嘯叫NVH問題途徑
1 故障車NVH測試
對下線車進(jìn)行主觀評價(jià):組織相關(guān)專家對66#車進(jìn)行主觀評價(jià),主觀感受車輛存在明顯的變速箱嘯叫;車輛在一級齒輪主階次、二級齒輪主階次和一#2級反拖主階次都出現(xiàn)嘯叫較嚴(yán)重NVH問題,不可接受。
在66#整車上對變速箱噪音信號進(jìn)行采集,66#測試數(shù)據(jù)如圖2所示。
圖2 WOT運(yùn)動模式加速車內(nèi)噪聲
從圖中可知,嘯叫現(xiàn)象主要出現(xiàn)在WOT全油門加速工況:一級22階次1 500~3 500 r/min、 4 500~6 000 r/min、7 000~8 000 r/min、9 000~10 000 r/min段,二級齒輪6.16階次3 000~ 6 000 r/min,出現(xiàn)階次造成超標(biāo)、嘯叫等NVH問題;測量數(shù)據(jù)表明一級和二級主階次對嘯叫NVH噪聲的貢獻(xiàn)較大。
2 電驅(qū)動減速器NVH問題原因分析
減速器NVH問題產(chǎn)生的因素很多,NVH—噪音、振動、模態(tài)分析[1-2],識別減速器NVH噪音問題的影響因素進(jìn)行分解,如圖3所示。
減速器NVH問題主要表現(xiàn)為齒輪嘯叫問題,通過對激勵、路徑和響應(yīng)進(jìn)行故障問題分析,本文主要從激勵源齒輪副嚙合噪聲特性研究分析[3],產(chǎn)生齒輪嚙合的嘯叫可能因子分解,如圖4所示。
綜上,電驅(qū)動減速器NVH問題主要問題有:1)齒輪宏觀參數(shù)指標(biāo)優(yōu)化重新設(shè)計(jì);2)齒輪微觀修形的優(yōu)化重新設(shè)計(jì)。
3 減速器齒輪參數(shù)優(yōu)化設(shè)計(jì)
3.1 齒輪宏觀參數(shù)優(yōu)化設(shè)計(jì)
通過優(yōu)化齒輪宏觀參數(shù),在保證滿足齒輪強(qiáng)度下,通過減小齒輪模數(shù)、增加齒數(shù)、提高齒頂高系數(shù)和增大螺旋角方向,提高端面和軸向重合度,實(shí)現(xiàn)減小傳遞誤差。眾所周知,齒輪嚙合重合度越大,單個(gè)齒所受的載荷越小,傳動越平穩(wěn),傳遞誤差越小,所以通過增加端面重合度、軸向重合度和總重合度來減小傳遞誤差,這是減速器解決NVH噪音問題優(yōu)化齒輪宏觀參數(shù)的主要目的,如表1所示。
圖3 減速器NVH問題影響因素
圖4 減速器嘯叫產(chǎn)生的可能因子分解
表1 減速器一、二級齒輪副宏觀參數(shù)優(yōu)化前后對比
3.2 微觀修形優(yōu)化設(shè)計(jì)
目前純電動汽車扭矩需求越來越大,同時(shí)扭矩使用較寬,又因制造和安裝誤差、軸系的彎曲扭轉(zhuǎn)變形、齒輪的受載彈性變形、熱變形、軸承游隙等復(fù)雜因素的影響,導(dǎo)致減速器齒輪的齒形偏離理論輪廓,造成嚴(yán)重的載荷集中現(xiàn)象,從而加劇NVH嘯叫噪音。另一方面,純電動車速也越來越高,齒輪傳遞的功率相應(yīng)增大,因此,運(yùn)轉(zhuǎn)中會增加熱變形,使得齒輪副的嚙合偏離理論輪廓,從而增加傳遞誤差。這時(shí),需要對齒輪進(jìn)行微觀修形,補(bǔ)償實(shí)際嚙合與理論嚙合之間的偏離,能有效優(yōu)化減速器的嘯叫噪音NVH問題。齒輪修形可分為修緣、鼓形、端面修形和角度修形。受載齒輪在單對齒嚙合時(shí),輪齒會因彈性變形而產(chǎn)生基節(jié)誤差。另外,齒輪還存在制造上的基節(jié)誤差,嚙入嚙出存在沖擊,嚴(yán)重影響齒輪傳動平穩(wěn)性,為了消除這種嚙入嚙出沖擊干涉,考慮磨齒工藝性和加工成本,常用對齒頂進(jìn)行修緣。由于齒輪運(yùn)轉(zhuǎn)系統(tǒng)的變形和其制造、安裝上的誤差,齒輪嚙合時(shí)載荷沿齒面接觸線的分布是不均勻的。如果齒輪軸不平行或其他原因造成軸兩邊的彎曲變形不等時(shí),則會發(fā)生齒端局部接觸現(xiàn)象,出現(xiàn)載荷集中的現(xiàn)象。為避免上述兩個(gè)現(xiàn)象,減輕嚙合沖擊,進(jìn)行齒向端面修形。經(jīng)修鼓形量的齒輪嚙合接觸會先發(fā)生在靠近齒寬中間部分,然后再過渡到全齒寬上,有利于齒面上的載荷分布均布,并能提高齒輪的疲勞壽命,降低NVH噪音問題。在產(chǎn)品開發(fā)初期,考慮NVH開發(fā)[4-5],首先用Masta軟件建模,把齒輪、軸、差速器殼體進(jìn)行有限元畫網(wǎng)格處理,其次把電驅(qū)動單元(Electric Drive Unit, EDU)三合一總成殼體進(jìn)行有限元處理,把殼體有限元整體導(dǎo)入Masta模型中,再按照客戶或成熟產(chǎn)品常用載荷譜進(jìn)行微觀修形優(yōu)化設(shè)計(jì)仿真,如圖5所示,對齒頂進(jìn)行修緣,同時(shí),在齒形、齒向方向上分別進(jìn)行鼓形量(Ca, Cβ)及齒形、向角度誤差(fHα, fHβ)進(jìn)行修形,以達(dá)到傳遞誤差TE降低。TE目標(biāo)值一級齒輪副<0.25,二級齒輪副<0.5,齒輪接觸斑點(diǎn)中心應(yīng)位于齒高H*40%和齒寬B*40%形成的矩形區(qū)域內(nèi)為設(shè)計(jì)目標(biāo)。
圖5 Masta建模仿真
3.2.1修形結(jié)果
表2 減速器一、二級齒輪副微觀參數(shù)優(yōu)化前后對比
觀修形優(yōu)化前后微觀參數(shù)對比,T1和T2是優(yōu)化前,T3是優(yōu)化后結(jié)果,如表2所示。
微觀修形優(yōu)化前后TE數(shù)值對比,T1和T2是優(yōu)化前、T3是優(yōu)化后,一、二級齒輪副TE值優(yōu)化前后對比,如圖6和圖7所示。
接觸斑點(diǎn)優(yōu)化前后對比,優(yōu)化后的接觸斑點(diǎn)更居中,有利于齒輪接觸疲勞強(qiáng)度,如圖8和圖9所示。
圖6 一級齒輪副優(yōu)化前TE對比
圖7 二級齒輪副優(yōu)化后TE對比
圖8 優(yōu)化前接觸斑點(diǎn)
圖9 優(yōu)化后接觸斑點(diǎn)
3.3 齒輪軸承強(qiáng)度校核
齒輪、軸承強(qiáng)度校核滿足設(shè)計(jì)要求,齒輪齒面接觸疲勞強(qiáng)度安全系數(shù)>1.0,齒輪齒根彎曲疲勞強(qiáng)度安全系數(shù)>1.2,軸承損傷率<100%,如圖10和圖11所示。
圖10 優(yōu)化后齒輪強(qiáng)度校核結(jié)果
圖11 優(yōu)化后齒輪軸承強(qiáng)度校核結(jié)果
4 優(yōu)化樣機(jī)測試評價(jià)
4.1 EDU總成搭載整車
按照新的齒輪宏觀、微觀參數(shù)試制齒輪軸零件,裝配EDU總成樣機(jī),再把EDU總成搭載整車。
4.2 整車主觀駕評
齒輪宏觀參數(shù)和微觀修形參數(shù)優(yōu)化后方案T3,第一級齒輪(27階)較原方案(22階)優(yōu)化明顯,第二級齒輪諧波優(yōu)化也較明顯,反拖工況主要問題的第一級齒輪T3的27階次噪音也較原(22階)優(yōu)化明顯。
4.3 整車NVH測試
圖12 測試傳感器布置位置
在整車NVH測試中,傳感器布置如圖12所示。
4.4 齒輪宏觀參數(shù)和微觀參數(shù)優(yōu)化前后NVH性能對比
圖13 優(yōu)化前后齒輪嚙合階次線
圖14 優(yōu)化前后車內(nèi)噪音階次切片的對比曲線
齒輪優(yōu)化前后,整車NVH測試結(jié)果如圖13和圖14所示。
4.5 整車NVH測試結(jié)論
通過齒輪宏觀參數(shù)和微觀修形參數(shù)優(yōu)化后的方案(深色曲線),第一級齒輪(27階)較原方案(22階)大幅優(yōu)化(減小20 dBA),第二級齒輪諧波減小10 dBA。反拖工況,主要問題為第一級齒輪27階次噪音,針對該問題,優(yōu)化后的方案較原方案大幅優(yōu)化(減小15 dBA)。
5 結(jié)語
以整車嘯叫NVH問題作為減速器的故障表現(xiàn)形式,通過對故障車NVH測試以及階次分析,識別出主要噪聲階次。通過以上齒數(shù)、模數(shù)、齒頂高系數(shù)、齒寬等宏觀參數(shù)優(yōu)化,特別進(jìn)行細(xì)高齒優(yōu)化設(shè)計(jì),其目的都是提高齒輪的重合度,同時(shí)通過Masta軟件建模仿真修形,對齒頂修緣、齒形、齒向角度修形及鼓形量等微觀參數(shù)優(yōu)化設(shè)計(jì),實(shí)現(xiàn)減小傳遞誤差、增大重合度,經(jīng)過以上優(yōu)化驗(yàn)證很好地改善齒輪嚙合區(qū)域,減小傳遞誤差,此方案對于解決純電動高速電驅(qū)EDU總成NVH問題效果較佳,最終得到客戶的認(rèn)可,實(shí)現(xiàn)量產(chǎn),也為純電動汽車高速EDU減速器NVH性能工程化優(yōu)化提供一種思路。
審核編輯:湯梓紅
-
減速器
+關(guān)注
關(guān)注
7文章
393瀏覽量
23246 -
純電動汽車
+關(guān)注
關(guān)注
5文章
464瀏覽量
25658 -
NVH
+關(guān)注
關(guān)注
2文章
62瀏覽量
10094
原文標(biāo)題:探究丨純電動三合一電驅(qū)總成NVH問題的方法
文章出處:【微信號:EDC電驅(qū)未來,微信公眾號:EDC電驅(qū)未來】歡迎添加關(guān)注!文章轉(zhuǎn)載請注明出處。
發(fā)布評論請先 登錄
相關(guān)推薦
純電動汽車電驅(qū)動總成NVH分析與優(yōu)化研究
三合一電驅(qū)系統(tǒng)可靠性試驗(yàn)研究與應(yīng)用
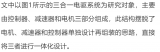
三合一電驅(qū)系統(tǒng)可靠性試驗(yàn)研究與應(yīng)用
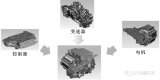
移動電源方案究竟硬件三合一還是軟件三合一?
同步整流 移動電源三合一問題
移動電源硬件三合一方案和軟件三合一方案對比
新人提問:移動電源方案軟件三合一好還是硬件三合一好?
最新電動牙刷三合一智能芯片方案
移動電源三合一方案都有哪些_移動電源三合一方案哪種最穩(wěn)定
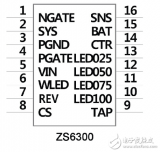
三合一電驅(qū)系統(tǒng)概述與可靠性試驗(yàn)技術(shù)要求的選擇與應(yīng)用
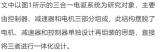
新能源乘用車三合一電驅(qū)動系統(tǒng)的結(jié)構(gòu)方案及電氣原理
高性價(jià)比三合一移動電源設(shè)計(jì)技術(shù)
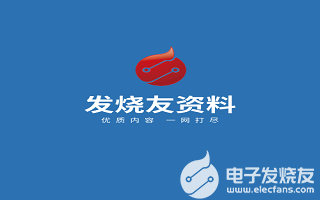
評論