電路板的焊接是電子產(chǎn)品制造過程中非常重要的一步。一個良好的焊接是保證電子產(chǎn)品正常運行的基礎,因此在焊接過程中需要掌握一些方法和技巧,以確保焊接質量和效果。下面將詳細介紹電路板焊接的方法和技巧。
一、材料準備
在焊接之前,首先需要準備好相應的焊接材料,包括焊錫絲、焊錫膏、焊接助劑等。焊錫絲是最基本的焊接材料,一般選擇質量好、熔點適中的焊錫絲。焊錫膏和焊接助劑可以提高焊接效果,其中焊膏能夠提供焊摩擦劑,減少焊錫劑的氧化,加速熔化;焊接助劑可以提供保護層,防止環(huán)境中的氧氣和其他雜質對焊接的影響。
二、焊接設備準備
在焊接之前,需要將焊接設備準備好。焊接設備主要包括焊接臺、焊接臺燈、焊錫臺等。焊接臺需要選擇平整、不易受熱變形的材質,焊接臺燈是為了提供足夠的光線,使焊接處能夠清晰可見。
三、焊接前的準備工作
在焊接之前,需要進行一些準備工作。首先,要對焊接的電路板進行清潔處理,確保焊接點和電路板表面光潔??梢允褂孟窗逅蛘呔凭M行清潔。其次,需要準備好焊接輔助工具,比如錫吸器、拉錫線等。焊錫吸器可以用來處理焊錫過多或者焊接錯誤的情況,拉錫線可以用來處理焊接厚度不均勻的地方。
四、焊接技巧
1.選擇適當?shù)暮稿a絲直徑:一般來說,焊錫絲的直徑越小,焊接的精度越高。但是過細的焊錫絲容易造成焊接點的不穩(wěn)定,因此需要根據(jù)實際情況選擇合適的焊錫絲直徑。
2.掌握適當?shù)暮附訙囟群蜁r間:焊接溫度過高會導致焊點容易熔斷,溫度過低則會導致焊點不牢固。因此需要根據(jù)焊錫絲的熔點和焊接材料的要求,掌握適當?shù)暮附訙囟群蜁r間。
3.保持穩(wěn)定的手持和焊接速度:在焊接的過程中,需要保持穩(wěn)定的手持和焊接速度,以確保焊接點的質量和均勻性。手持不穩(wěn)定會導致焊接點錯位或者焊接不均勻,焊接速度過快則會導致焊接點質量下降。
4.注意焊接時的環(huán)境干凈度:焊接時的環(huán)境干凈度對焊接點的質量有直接影響。在焊接之前,要確保環(huán)境中沒有灰塵、油污等雜質,以免影響焊接效果。
5.注意焊接時的安全防護:焊接是一項需要注意安全的工作。首先,要注意焊接過程中的溫度,避免燙傷。其次,要注意焊接時的煙霧和氣味,盡量選擇通風良好的環(huán)境或者佩戴適當?shù)姆雷o設備。
總結起來,電路板的焊接是一項技術含量較高的工作,要求焊接人員具備一定的經(jīng)驗和技巧。當然,在實際操作中還需要根據(jù)具體情況進行調整和提升,不斷總結和積累經(jīng)驗,以提高焊接質量和效果。
-
電路板
+關注
關注
140文章
4951瀏覽量
97687 -
焊接
+關注
關注
38文章
3114瀏覽量
59695 -
焊錫
+關注
關注
0文章
257瀏覽量
18124 -
焊膏
+關注
關注
0文章
43瀏覽量
10379
發(fā)布評論請先 登錄
相關推薦
PCB雙面回焊制程(SMT)介紹及注意事項
柔性電路板焊接方法操作步驟和注意事項
柔性電路板焊接方法操作及焊接過程中需注意的問題
雙面電路板焊接方法視頻
雙面電路板的焊接方法
波峰焊和浸焊對比,都具有哪些的優(yōu)缺點
柔性電路板的焊接方法和注意事項
波峰焊給電子行業(yè)帶來了哪些益處
印制電路板的最佳焊接方法
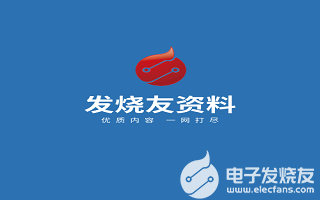
PCB印制電路板的焊接方法
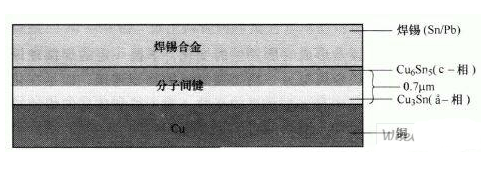
評論